SG EBS Transformation through Continuous Improvement & Innovation
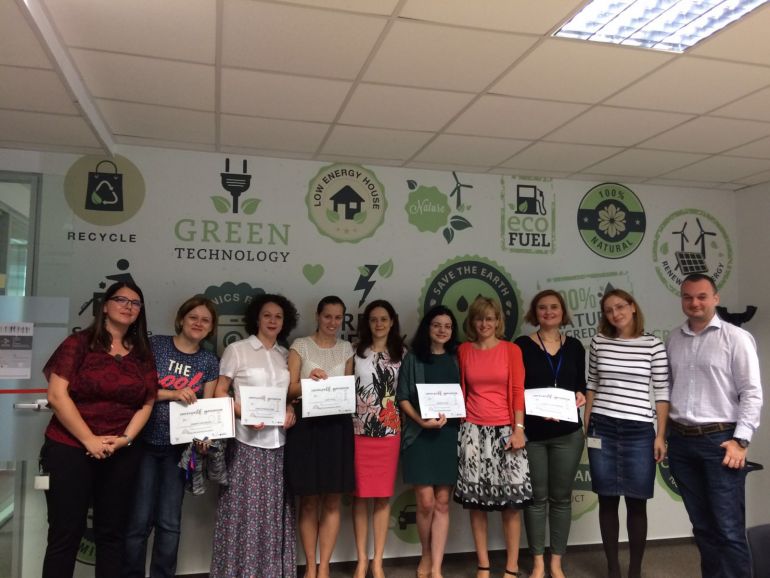
Citește în continuare

For SGEBS, the Continuous Improvement journey has started 4 years ago, when a couple of great minds decided to change the future of the Shared Service Center, standardize the processes and improve on behalf of our Customers.Â
One of the strategic directions of SG EBS right from the beginning was to focus on the service quality and continuous improvement. The Continuous Improvement culture is supported at all levels, starting from the operational level to the top management level, the teams being included in Lean Six Sigma Yellow, Green and Black Belt training workshops.
Nowadays SGEBS has a Continuous Improvement Project Management Team focusing all efforts on three main areas: HR, Finance and IT Services offered to our Clients.
During the past years, our team’s ambition was to foster the Continuous Improvement spirit within the company, use the Lean Six Sigma tools to improve the quality of our services and achieve Service Center of Excellence.
In 2015, 60% of all employees were trained on Lean Six Sigma Yellow Belt, the basics. Our goal 2016 is to have 80% of all our employees trained.
In parallel, we have developed a program called IDEA that encourages everyone to participate with process improvement ideas. We accept ideas that contribute to the operational efficiency increase and quality or customer experience improvement. The employee active involvement has a positive impact on their motivation to participate to the standard work transformation. In the implementation phase, the teams are coached by our project managers who evaluate the benefits and impacts in the process and help the teams get to the implementation phase. The contributions are recognized and awarded upon project closure.
In 2015, we received 400 ideas; we implemented 70% of them, accounting for 600 hours saved.
In 2016 our ambition is to have 50% of all employees submit and implement at least one IDEA.
Therefore, delivering high quality services is less challenging, as new ideas generated innovation and innovation generated high impact initiatives.
The HR Continuous Improvement Team works closely with the internal departments on several initiatives:
- Six Sigma Yellow Belt sessions for all employees to get them introduced to Lean Six Sigma methodology, generate process improvement IDEAs and be a constant support for their teams;
- IDEA Program for generating and implementing improvement initiatives at all levels, encouraging all employees to submit and implement ideas awarded quarterly during celebration meetings;
- Mentoring Lean Six Sigma Yellow Belt & Green Belt Projects aiming to improve the quality of our services and helping the Team put into practice the elements learned during the LSS Trainings; our goal is to use the Lean Six Sigma methodology to bring significant improvement and inspire others to conduct similar projects;
- Other initiatives coordinated with the SG EBS management and employees:Â Quality workshops, Operational assessments, Process auditing
At SG EBS our Continuous Improvement Project Managers inspire the Teams to strive for continuous improvement each and single day, think outside the box, experiment and not be afraid to step outside the comfort zone for innovative solutions.
The next level towards SGEBS is heading is the Innovation and Automation of transactional activities, a field towards the entire Shared Service Center field is heading. By automation we mean applying new technologies on chosen activities and using Lean as a second layer to test and standardize management practices.
The disruptive changes in the organization will have an effect on the profile portfolios that the company will recruit in the future. Stay tuned for more updates from us.
                             by    SG EBS – SSC HR Continuous Improvement Team
OTHER EVENTS THAT MIGHT INTEREST YOU